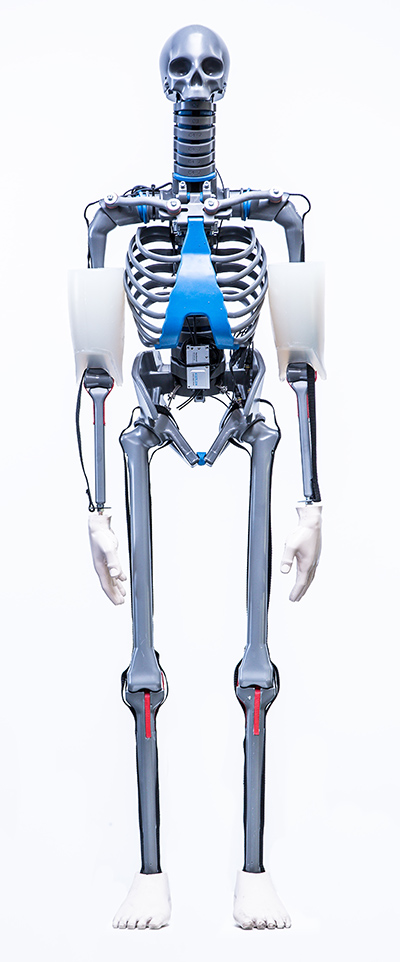
Wie verhält sich der menschliche Thorax unter der Einwirkung von dynamischen Lasten? Eine Frage, die für viele Forschungsgebiete von entscheidender Bedeutung ist. Sei es bei der Erschließung neuer Sicherheitstechnologien im Bereich Automotive oder dem Erproben neuer Schutzkleidung in der Verteidigungsforschung. Forschende am EMI arbeiten an Möglichkeiten, um die Ergebnisse aus solchen Tests genauer und aussagekräftiger zu machen.
Die Weiterentwicklung von Dummys mittels additiver Fertigung
Dieses Ziel soll durch die Weiterentwicklung eines neuen, innovativen Dummys, dessen Knochenstrukturen möglichst optimal dem menschlichen Vorbild nachempfunden sind, erreicht werden. Der Herausforderung des Herstellens von Rippenknochensurrogaten mittels 3D-Druckverfahren stellen sich Marcin Jenerowicz aus der Arbeitsgruppe »Human Body Dynamics« und weitere Wissenschaftler:innen aus der Gruppe »Additive Design and Manufacturing« des Ernst-Mach-Instituts. Die Surrogate sollen Informationen darüber geben, wann und unter welchen Krafteinwirkungen Strukturen des menschlichen Thorax Schäden erleiden.
Der PRIMUS Breakable Dummy der Firma Crashtest-Service GmbH (CTS) wird bereits in verschiedenen Bereichen als anthropomorphes Testgerät eingesetzt. Der CTS Dummy (50-Perzentil-Mann-Surrogat / M-50) ist in der Lage, authentische Fahrzeugschäden sowie Schäden an seinen eigenen strukturellen Komponenten darzustellen, um eine Übereinstimmung zwischen Dummy-Schäden und Verletzungswahrscheinlichkeit zu finden. Bislang wurden jedoch nur Validierungstests im Crash-Bereich durchgeführt, die die Validität und das globale strukturelle Verhalten (Flugbahn, Schäden an internen und externen Strukturen) des Dummys für bestimmte Unfallfolgen darstellen.