
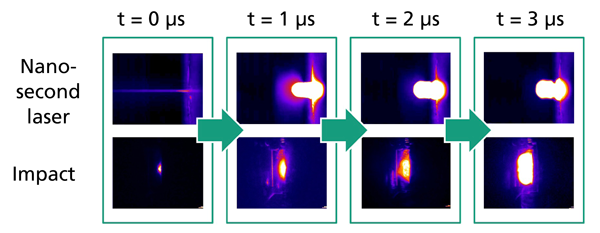
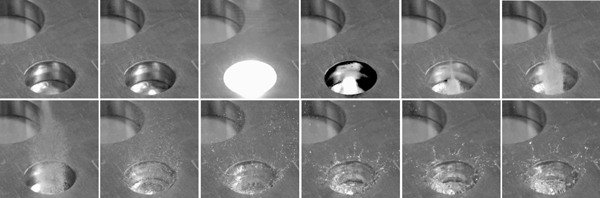
Fraunhofer EMI is currently setting up a new laboratory for applications in laser technology featuring powerful lasers, in which novel pulsed laser applications as well as continuous-wave (CW) laser applications can be developed and tested. The background for building this lab is the dramatic increase in the performance of commercially available compact, diode-pumped lasers, and in particular, also mechanically very robust and easy-to-use fiber lasers. The performance level of fiber lasers has increased significantly since 2000 and is now well above ten kilowatts.
Therefore, the use of lasers with new processing methods, such as laser cutters for cutting materials or laser welding for joining materials, has massively expanded. In all these established forms of material processing, the laser is used at short distances. However, lasers with high beam quality, in particular single-mode fiber lasers, are available that permit the directed transport of laser energy over long distances and thus facilitate new application methods. For example, the application of high-power lasers for the neutralization of improvised explosive devices in civilian environments has already been investigated within the framework of the EU security project ENCOUNTER at Fraunhofer EMI.
In 2012, Fraunhofer EMI established its Laser Technology Group to examine potential applications for such lasers. One of these applications is the 3D printing of metallic components, which are manufactured using so-called laser sintering systems. This technology had been considered by Fraunhofer EMI since 2013. In the meantime, this topic has experienced such a great demand that on January 1, 2017, an additional Additive Design and Manufacturing Group emerged from the Laser Technology Group. The Additive Design and Manufacturing Group will be operating their 3D printing systems in a newly designed laboratory.
The new high-performance laser laboratory on the other hand enables the investigation of the interaction of laser radiation with materials. In the experiments, the irradiation leads to a directed energy transfer from the laser beam to the target. With the available high-power continuous-wave lasers, an energy input comparable to the kinetic energy of projectiles accelerated by EMI’s light-gas guns is achieved with irradiation durations of several seconds. In order to make clear that such intensive exposure is no longer comparable with a laser pointer, which does not modify the material, we speak of “laser impact” instead. However, regarding the physical process, it is important to note that although a high energy is coupled into a target with continuous-wave lasers, there is no momentum transfer, which is normally responsible for the strong mechanical forces during a projectile impact. The laser beam merely transfers a comparably high amount of energy in the form of thermal energy at the boundary surface of the target. Depending on the target material, processes such as ablation, heat conduction, softening, melting, chemical reactions etc. occur. Depending on the structure and design of the target, with continuous-wave lasers, a complex sequence of effects can result over the relatively long exposure times. This results in new challenges for models and simulations for the description of such processes.
In contrast to an impact process, it is interesting that in a continuous-wave laser experiment, the interaction with the target can influence the energy coupling during the irradiation period. As an example, Figure 1 shows a plasma plume which is generated during the irradiation process and which absorbs a part of the laser beam. It is therefore important to consider these effects in the models describing the energy input into the sample.
For the case of pulsed lasers, the formation of a plasma plume and the resulting effects have been experimentally used for many decades to generate shock waves. Lasers with pulse durations in the nanosecond range are often used for this purpose. The energy input occurs at the surface of the target. The target material evaporates and is transferred to the plasma state, where the material is in a partially ionized state. The plasma formation is accompanied by the short-time emission of light, similar to the impact flash that can often be observed during hypervelocity impact of projectiles. In Figure 2, the effect of such a laser pulse is compared with an impact experiment.
A useful tool for the scientific analysis of these processes is the measurement of the free electrons’ state in the plasma. At EMI, the corresponding technique for the measurement of electron temperature and density had already been developed for hypervelocity impact experiments. This technique was successfully applied to the measurement of laser-pulse generated plasma and was presented by Dominic Heunoske at the 11th International High Power Laser Ablation and Directed Energy Symposium, Santa Fe, USA, in April 2016.
How much the effect of a laser pulse resembles an impact process is also shown in an experiment in which the laser radiation was coupled into the interface of a water and metal layer (see Figure 3). In general, pulsed lasers can be used to investigate the behavior of materials at high-dynamic compressive loads in laser shock-wave experiments. In analogy to these pulsed laser applications, first tests on the possible use of how high-power continuous-wave lasers in new interdisciplinary research approaches for the characterization of transient melting processes have already been carried out at Fraunhofer EMI.