Primary development of process parameters for 3D printing of heavy metals and unique materials
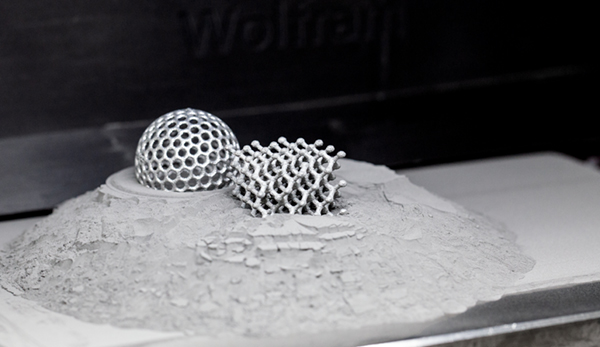
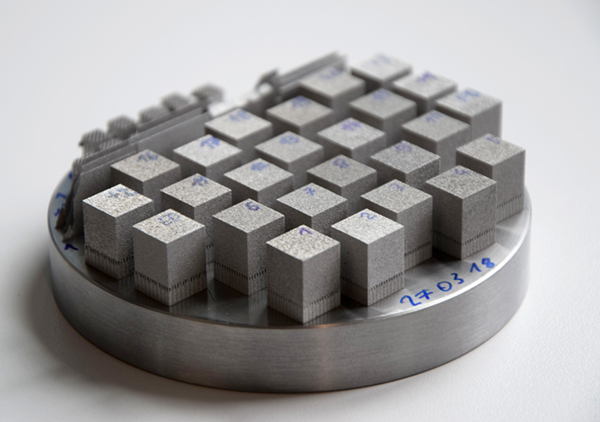
Additive manufacturing (3D printing) technology has experienced a rapid progress within the last years and is increasingly applied in the industry for small-series production. Due to the various fields of application, the material portfolio of the versatile 3D printing technologies is continuously growing. With its particularly distinctive material flexibility, the Laser Beam Melting (LBM) technology is the most widely used method for 3D printing of metals. Thin layers of metal powder are applied to a substrate, melted locally through laser energy and are fused with the previous layer. This way, a three-dimensional object is created from multiple layers, and a new freedom of design results from this additive principle. Furthermore, complex geometries can be generated for materials that, e.g. because of their hardness, are very difficult to process. Other advantages of LBM are flexibility, the opportunity of integral design, integration of functions, improved logistics, reduced development times, and individual products. Essentially, in comparison with conventional methods, LBM offers comparable material density and excellent material properties. This technology is particularly suitable for the manufacturing of highly loaded machine parts optimized in terms of lightweight design, or for functional applications in defense technology.
Few alloys serve specific fields of application
Due to the currently complex and expensive parameter development for new alloys for LBM-based 3D printing, only few selected alloys are used for a wide range of applications. Aluminum and titanium alloys address the lightweight design sector. Nickel alloys are suitable for high temperature applications, stainless steel for engineering and the manufacturing of art objects. Cobalt chrome and titanium alloys serve the medical engineering market, and high-strength steels are used for the production of tools. However, fields of application with a need for alternative materials have yet only been covered to a limited extent. Especially for dynamic applications, such as car crashes and, particularly, defense technology, there are currently no suitable materials commercially available. At Fraunhofer EMI, we thus develop our own manufacturing parameters for the processing of special materials. The defense sector of armor and effect is a particular focus in this development.
Additively manufactured high quality heavy metals
At EMI, parameters for the manufacturing of high quality tungsten have been developed. Tungsten is characterized by its high density and the highest melting point of all metals. The manufacturing of refractory metals such as tungsten shows that with the LBM method, even metals that are difficult to machine with conventional methods can be processed, even though they are considered to be difficult to weld and the LBM method basically resembles a laser welding process. During the parameter development for tungsten, the EMI scientists were faced with special challenges. Due to the high local energy application and resulting rapid cooling rates during the processing of the material by a laser beam, cracking occurs in the microstructure. The formation of micro cracks was successfully minimized during the studies. The result is a brittle material with a density of approximately 19.2 grams per cubic centimeter, an additively manufactured, pure tungsten with strongly reduced micro cracks and optimized density. This material can for example be used for ammunition or special applications such as collimators for X-ray detectors. Further fields of application are electrical engineering, medical engineering, and domains with extreme thermal requirements.
Efficient parameter development and optimization with in-house methodology
For the development of parameter sets, an efficient in-house solution is used, which allows a comparably fast and simple development of the process parameters. This way, particularly expensive special materials can be generated more cost-effectively. The method is based on the observation of the interaction between the laser beam and the metal powder as well as on a statistical experimental design. The obtained findings are later used for the application-specific parameter optimization and the parameter adaptation for specific structural components and their manufacturing requirements. For initial characterizations of the resulting materials, fast techniques, such as density determination, are applied. If the parameter set is well-developed, the material is characterized using the latest measuring technology (e.g. electron backscatter diffraction (EBSD) or micro CT imaging), and the parameters are further refined.
The use of an in-house methodology for parameter development for LBM materials allows the efficient generation of manufacturing parameters, and thus, the use of optimized materials for specific fields of application. We have shown that with this method, even materials that are difficult to process can be produced in high quality. It is conceivable that in the future, novel alloys can be elaborated that cannot be realized with conventional methods. For example, the high cool-down rate of the process might facilitate a higher solubility of alloy elements and, thus, new material properties. For the choice of future alloys, we do not only have to take into account the field of application but also the extended possibilities regarding the new freedom of design. Conventionally, requirements are for example met using geometries based on semi-finished products, (e.g. plates), whereas in additive methods, the solutions can be more efficient thanks to alternative geometries (e.g. lattice structures). A suitable material has to be chosen based on the new geometry.